Carbon Black Blog
Effect of Carbon Black Dispersibility on Coating Viscosity
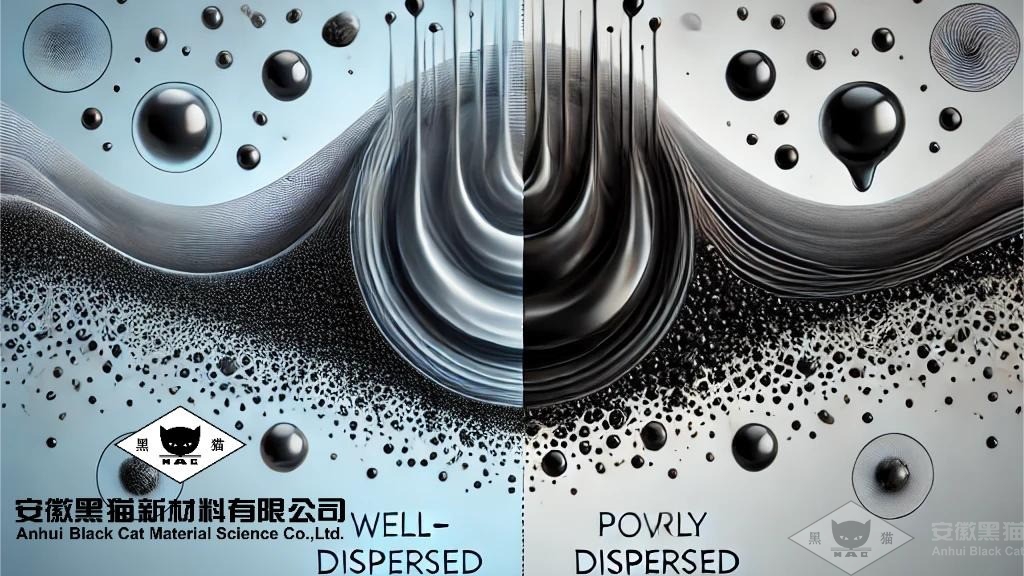
Carbon black is widely used in coatings due to its excellent tinting strength, UV absorption capacity, and conductivity, making it an indispensable component in coatings. However, during the dispersing process of carbon black, issues such as high viscosity and low fluidity can arise in the finished coating, affecting the entire production process and product quality. Through application tests conducted in our lab, we have identified several factors that influence the viscosity and fluidity of coatings
Topics: #pigmentcarbonblack #carbonblackdispersion #coatingviscosity
1. Factors Related to Carbon Black
1.1 Structure and Surface Area
The structure and specific surface area of carbon black are key factors affecting its dispersibility. A lower structure and larger specific surface area can increase the van der Waals forces between carbon black particles, making them easier to agglomerate and harder to disperse, which results in higher system viscosity. Therefore, selecting carbon black with the appropriate structure and surface area is crucial for ensuring better dispersibility and maintaining suitable system viscosity.
1.2 Surface Activity
The surface activity of carbon black also significantly impacts its dispersibility in coatings. Functional groups on the surface of carbon black, such as carboxyl and hydroxyl groups, can enhance its compatibility with the coating system, improving dispersibility. Anhui Black Cat has a post-treatment production line that optimizes the surface properties of carbon black, allowing for better dispersibility in coatings.
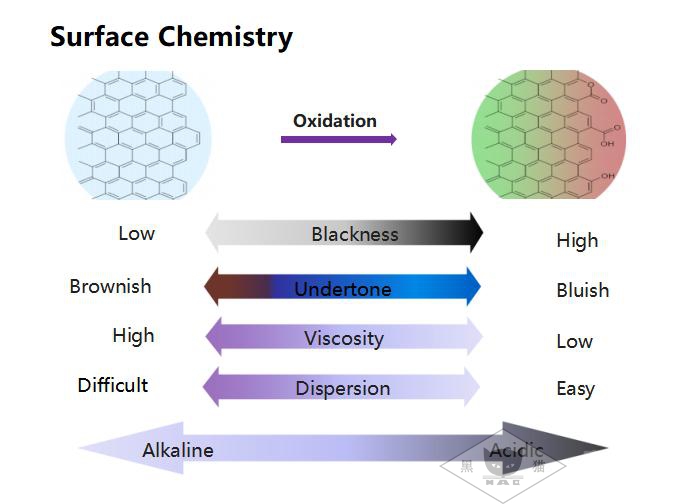
2. Selection of Dispersants
Dispersants play a crucial role in the dispersibility of carbon black. They work by attaching to the surface of carbon black particles, reducing the attractive forces between particles and preventing agglomeration. Choosing the right dispersant can improve the viscosity of the carbon black system and reduce the flow resistance of the dispersion. It is essential to control the amount of dispersant used, as excessive use may lead to overly high system viscosity.
3. Dispersing Equipment
The choice of dispersing equipment significantly affects the ease of dispersing carbon black. Common dispersing equipment includes high-shear dispersers, ball mills, sand mills, and three-roll mills. By selecting the appropriate equipment and operating parameters, a uniform dispersion of carbon black can be achieved.
4. Compatibility of Resin
The compatibility between resin and carbon black is another critical factor affecting dispersibility. Incompatible resins can result in poor wetting of carbon black, leading to inadequate dispersion. When selecting resin, its chemical properties and polarity should be considered. Compatibility tests should be conducted, and the formulation adjusted accordingly to enhance the dispersibility of carbon black.
5. Carbon Black Concentration
Higher loading of carbon black can increase system viscosity, reducing fluidity. Maintaining a reasonable concentration of carbon black and an appropriate proportion of other ingredients is crucial for achieving suitable fluidity.
6. Solvent Selection
In solvent-based coatings, the choice of solvent directly affects the dispersibility of carbon black. A solvent with appropriate dissolving power can improve the wetting and stability of carbon black, leading to better dispersion. The solvent should be selected based on its compatibility with the resin and carbon black to ensure the stability and uniformity of the coating system.
7. Process Conditions
Process conditions such as temperature, mixing speed, and loading sequence also influence the dispersibility of carbon black. Higher temperatures can lower the viscosity of the coating, promoting the dispersion of carbon black, but excessively high temperatures may cause adverse reactions or degradation of coating ingredients. Optimizing process parameters is necessary to achieve the best dispersion effect.
Solutions to Address the Above Issues:
- 1. Selection of Carbon Black: Choose the appropriate type of carbon black according to system requirements.
- 2. Optimization of Dispersant: Select dispersants suitable for the coating formulation and control the amount used reasonably.
- 3. Dispersing Equipment: Use a high-shear mixer or bead mill to achieve finer dispersion.
- 4. Formulation Adjustment: Adjust the combination of resin, solvent, and additives; reasonably match the amount of carbon black added, and improve overall dispersion quality.
- 5. Process Optimization: Adjust processing parameters such as mixing speed, temperature, and material loading sequence to ensure optimal dispersion.
Carbon black dispersion issues are common technical challenges in the application of carbon black. However, through the reasonable selection of dispersants, formulation adjustments, and process optimization, these issues can be effectively addressed. This will improve the stability and overall performance of carbon black dispersion systems, providing better technical support for the application of carbon black in related fields.
Anhui Black Cat owns the largest pigment carbon black application R&D center in China, enabling us to provide prompt and effective solutions to customer application problems. With over 200 application formulations, we can offer guidance on carbon black application and enhance its performance.
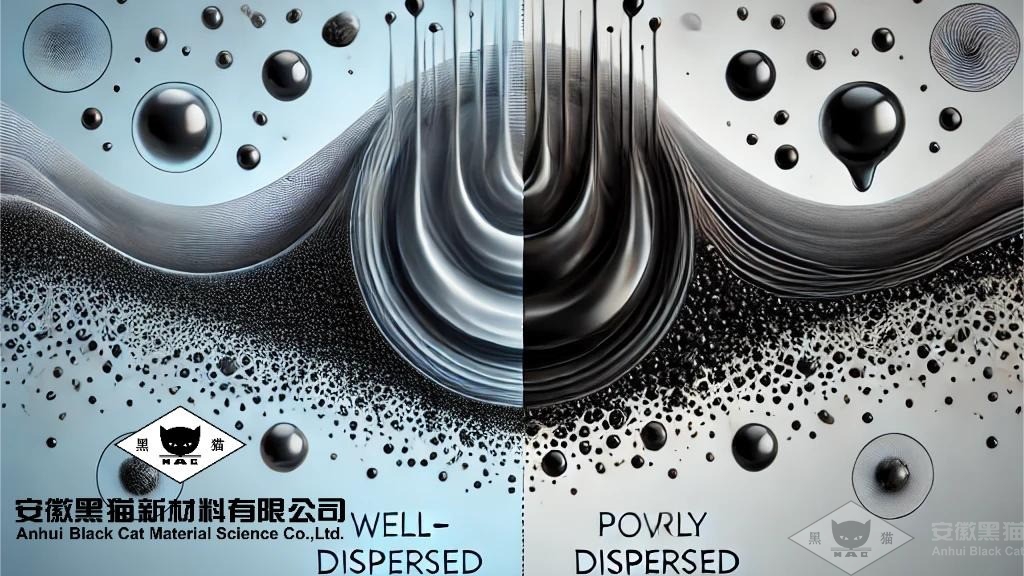
Carbon black is widely used in coatings due to its excellent tinting strength, UV absorption capacity, and conductivity, making it an indispensable component in coatings. However, during the dispersing process of carbon black, issues such as high viscosity and low fluidity can arise in the finished coating, affecting the entire production process and product quality. Through application tests conducted in our lab, we have identified several factors that influence the viscosity and fluidity of coatings
Topics: #pigmentcarbonblack #carbonblackdispersion #coatingviscosity
1. Factors Related to Carbon Black
1.1 Structure and Surface Area
The structure and specific surface area of carbon black are key factors affecting its dispersibility. A lower structure and larger specific surface area can increase the van der Waals forces between carbon black particles, making them easier to agglomerate and harder to disperse, which results in higher system viscosity. Therefore, selecting carbon black with the appropriate structure and surface area is crucial for ensuring better dispersibility and maintaining suitable system viscosity.
1.2 Surface Activity
The surface activity of carbon black also significantly impacts its dispersibility in coatings. Functional groups on the surface of carbon black, such as carboxyl and hydroxyl groups, can enhance its compatibility with the coating system, improving dispersibility. Anhui Black Cat has a post-treatment production line that optimizes the surface properties of carbon black, allowing for better dispersibility in coatings.
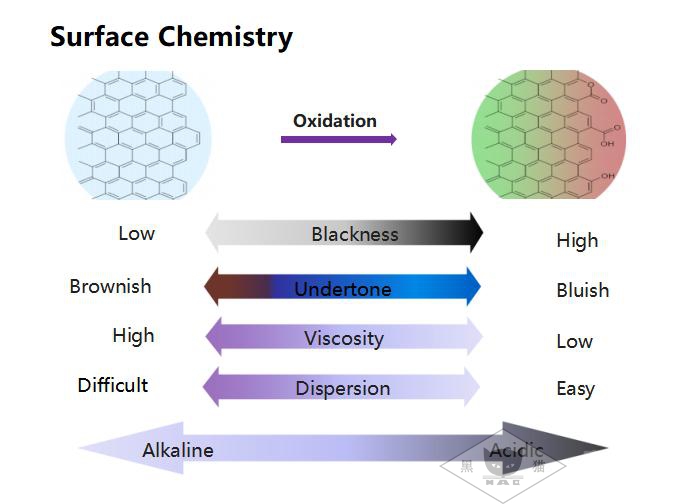
2. Selection of Dispersants
Dispersants play a crucial role in the dispersibility of carbon black. They work by attaching to the surface of carbon black particles, reducing the attractive forces between particles and preventing agglomeration. Choosing the right dispersant can improve the viscosity of the carbon black system and reduce the flow resistance of the dispersion. It is essential to control the amount of dispersant used, as excessive use may lead to overly high system viscosity.
3. Dispersing Equipment
The choice of dispersing equipment significantly affects the ease of dispersing carbon black. Common dispersing equipment includes high-shear dispersers, ball mills, sand mills, and three-roll mills. By selecting the appropriate equipment and operating parameters, a uniform dispersion of carbon black can be achieved.
4. Compatibility of Resin
The compatibility between resin and carbon black is another critical factor affecting dispersibility. Incompatible resins can result in poor wetting of carbon black, leading to inadequate dispersion. When selecting resin, its chemical properties and polarity should be considered. Compatibility tests should be conducted, and the formulation adjusted accordingly to enhance the dispersibility of carbon black.
5. Carbon Black Concentration
Higher loading of carbon black can increase system viscosity, reducing fluidity. Maintaining a reasonable concentration of carbon black and an appropriate proportion of other ingredients is crucial for achieving suitable fluidity.
6. Solvent Selection
In solvent-based coatings, the choice of solvent directly affects the dispersibility of carbon black. A solvent with appropriate dissolving power can improve the wetting and stability of carbon black, leading to better dispersion. The solvent should be selected based on its compatibility with the resin and carbon black to ensure the stability and uniformity of the coating system.
7. Process Conditions
Process conditions such as temperature, mixing speed, and loading sequence also influence the dispersibility of carbon black. Higher temperatures can lower the viscosity of the coating, promoting the dispersion of carbon black, but excessively high temperatures may cause adverse reactions or degradation of coating ingredients. Optimizing process parameters is necessary to achieve the best dispersion effect.
Solutions to Address the Above Issues:
- 1. Selection of Carbon Black: Choose the appropriate type of carbon black according to system requirements.
- 2. Optimization of Dispersant: Select dispersants suitable for the coating formulation and control the amount used reasonably.
- 3. Dispersing Equipment: Use a high-shear mixer or bead mill to achieve finer dispersion.
- 4. Formulation Adjustment: Adjust the combination of resin, solvent, and additives; reasonably match the amount of carbon black added, and improve overall dispersion quality.
- 5. Process Optimization: Adjust processing parameters such as mixing speed, temperature, and material loading sequence to ensure optimal dispersion.
Carbon black dispersion issues are common technical challenges in the application of carbon black. However, through the reasonable selection of dispersants, formulation adjustments, and process optimization, these issues can be effectively addressed. This will improve the stability and overall performance of carbon black dispersion systems, providing better technical support for the application of carbon black in related fields.
Anhui Black Cat owns the largest pigment carbon black application R&D center in China, enabling us to provide prompt and effective solutions to customer application problems. With over 200 application formulations, we can offer guidance on carbon black application and enhance its performance.